第五届全国称重技术研讨会论文集
重力式自动装料秤在冶金行业自动配料系统中的应用
济南金钟电子衡器股份有限公司 申颖
[摘要]针对冶金配料过程中遇到的问题,利用PLC,从硬件配置和逻辑控制角度,设计出一种新的配料系统,不仅节约了资金投入,也提高了工作效率。
关键词:PLC 冶金 自动配料
在冶金试验和生产过程中,经常会遇到多种不同的金属物料,以较大的配比值和较高的准确度进行配料。如表一为某企业的实际生产流程配料表:
配料 |
铁粉1 |
铁粉2 |
粗铝粉 |
中铝粉 |
细铝粉 |
铁合金1 |
铁合金5 |
铁合金2 |
铁合金3 |
铁合金4 |
铁合金6 |
生产100份
的配量
单位kg |
750 |
100 |
160 |
25 |
60 |
30 |
9 |
4 |
8 |
1 |
3.3 |
在配料过程中,各种配料重量悬殊较大;因为有下级混料装置,用户不关心瞬时配比,只要求配料过程中的计量准确度在0.1%范围内。
在方案设计中,不能只使用皮带秤进行动态称重配料,因为普通皮带秤的计量精度只有0.25%,为此,必须配置重力式自动装料秤。常规设计中,每种物料都需要配置一个承载称重料斗和称重显示仪表,不仅浪费资金,也浪费空间和时间,针对上述情况,考虑到每次称重100份的配量、称重次数和配料周期,特殊设计了配料系统。
1、系统工艺流程
给料设备由1#~11#11台振动给料机组成,定量称重料斗有1#~3#,量程分别为150kg、30kg、5kg。
第一组1#~3#振动给料机设置在量程为150kg的1#称重料斗上方,分别负责向1#料斗输送铁粉1、铁粉2、粗铝粉;第二组4#~7#给料机设置在量程为30kg的2#称重料斗上方,分别负责向2#料斗输送中铝粉、细铝粉、铁合金1、铁合金5;第三组8#~11#给料机设置在量程为5kg的3#称重料斗上方,分别负责向3#料斗输送中铁合金2、铁合金3、铁合金4、铁合金6。
振动给料机选用电机振动式,电机由变频器供电,当电机供电频率变化时,其给料流量随之变化,从而控制粗细给料。由于给料槽采用非金属材料,经过特殊处理,因此给料机在工作时不受金属物料流动的影响。
定量称重料斗装有称重传感器,将每一次称重结果送至称重显示仪。
集料斗将1#~3#定量称重料斗卸下的物料收集在混料器中,经过均匀混料的多种成分物料由皮带给料机送往定量称重斗4,再根据用户的要求进行定量。
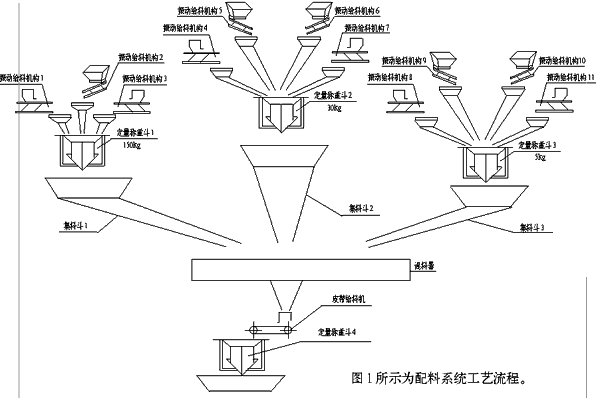
2.系统电气控制原理:
系统电气部分主要由称重传感器、称重显示仪表、可编程控制器(PLC)、变频器、工控机和打印机组成。如图2所示。
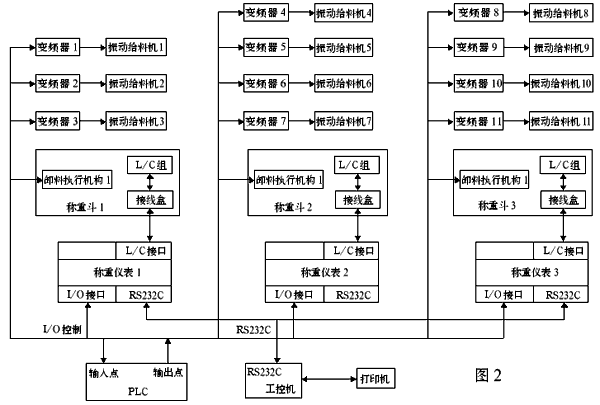
称重显示仪表为动态称重仪表,在动态称重过程中,接受定量称重料斗上称重传感器的重量信号。当料斗内的物料重量达到各设定值时,输出I/O定量信号给PLC。PLC采集称重显示仪表的定量输出信号,通过PLC控制每一台变频器的输出频率,从而控制相应振动给料机的粗细加料量及每一台称重料斗的开关料门动作。
工控机通过RS232接口与称重显示仪表通讯,将获得的每台秤的称重数据显示在监控画面上,用户可在称重显示仪表面板或工控机的操作界面上对配方进行调整。
系统的每一次配料工作过程中,利用PLC强大的逻辑控制功能,使11台振动给料机按一定逻辑采取顺序和同步两种工作方式,3台称重料斗也同时工作,节省了时间和成本。
3、配料过程
每次称重前,各定量称重料斗均放空物料,保持空秤静止状态,料斗门亦处于关闭状态。
首先,PLC发出启动信号给1#、4#、8#振动给料机变频器,开始分别对1#、2#、3#定量称重料斗进行定量配料。
3.1 1#称重料斗的配料过程:
1#定量称重仪表定量值先设为150kg, PLC对1#变频器发出启动和粗加料信号,则1#变频器控制1#振动给料机对1#定量称重料斗以较高频率进行铁粉1的粗加料,当铁粉1的重量值接近150kg时,1#称重仪表发出定量信号给PLC,PLC再通过1#变频器控制1#振动给料机较低频率进行细加料,当铁粉1的重量值达到150kg时,停止加料,秤体静止后,由PLC控制1#定量称重料斗的卸料、关料门,这样,就完成了一次称重过程。仍保持1#定量称重料斗定量值为150kg,如上循环五次称重过程,就完成了铁粉1的100份用量共750 kg的定量称重。
然后,PLC将1#定量称重料斗定量值改为100kg,启动2#给料机,称重一次,即完成了铁粉2的100份用量100 kg的定量称重。
接着,PLC将1#定量称重料斗定量值改为160kg,启动3#给料机,称重一次,即完成了粗铝粉的100份用量160 kg的定量称重。(见表2)
表2
工作顺序 |
给料机 |
设定值 |
称重次数 |
合计给料 |
1 |
1# |
150kg |
5次 |
750kg |
2 |
2# |
100kg |
1次 |
100kg |
3 |
3# |
160kg |
1次 |
160kg |
合计 |
|
|
7次 |
|
3.2 2#称重料斗的配料过程见表3
表3
工作顺序 |
给料机 |
设定值 |
称重次数 |
合计给料 |
1 |
4# |
25kg |
1次 |
25kg |
2 |
5# |
30kg |
2次 |
60kg |
3 |
6# |
30kg |
1次 |
30kg |
4 |
7# |
9kg |
1次 |
9kg |
合计 |
|
|
5次 |
|
3.3 3#称重料斗的配料过程见表4
表4
工作顺序 |
给料机 |
设定值 |
称重次数 |
合计给料 |
1 |
8# |
4kg |
1次 |
4kg |
2 |
9# |
4g |
2次 |
8kg |
3 |
10# |
1kg |
1次 |
1kg |
4 |
11# |
3.3kg |
1次 |
3.3kg |
合计 |
|
|
5次 |
|
当三台称重料斗都完成各自100份用量的定量称重后,系统也就完成了一次完整的配料过程。在这一过程中,1#定量称重料斗负责加料3种,共称重7次;2#定量称重料斗负责加料4种,共称重5次;3#定量称重料斗负责加料4种,共称重5次。各称重料斗在某次配料过程中的称重次数大体相当,都不会有太多的待机时间,较合理地利用了时间和资源。
4、PLC的电气连接和软件编制
以一套振动给料机的控制回路为例,PLC与二次仪表和变频器的接线如图3所示,某次配料工作过程PLC控制的一台称重料斗的程序流程如图4所示。
为确保系统运行的可靠性,下级皮带输送机的运行信号和集料器的已卸料信号应作为启动下一次配料的联锁信号;当某一台振动给料机或称重料斗因为意外故障停机时,PLC立即停止其余配料的给料,以便于检修,防止出现废料。
5、结束语
采用重力式自动装料秤组成配料系统的应用, 解决了在冶金试验和生产过程中,遇到的较大配比值、较高准确度与资金投入的矛盾,缩短了配料时间,提高了工作效率,增加了系统运行的可靠性,收效显著,值得推广。
<全文完>
|